Professioneller Service für unsere Kunden
Ihr Anliegen ist unsere höchste Priorität
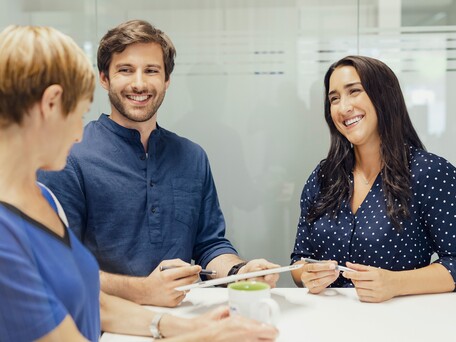
Wir bieten weltweit eine umfassende Palette an Serviceleistungen an, die von hoch qualifizierten Spezialisten durchgeführt werden. Dazu gehören technischer Support, Lieferung von Ersatzteilen, Wartung und jährliche Kalibrierung Ihrer BAUR Geräte, Reparatur bei eventuellen Defekten sowie Schulungen zur Nutzung unserer Geräte.
Unser Ziel ist es, Ihnen einen erstklassigen Kundenservice zu bieten, der auf Ihre individuellen Bedürfnisse zugeschnitten ist. Unsere Servicespezialisten verfügen über umfangreiche Fachkompetenz und jahrelange Erfahrung. Kontaktieren Sie uns, um einen Termin für Ihre Serviceleistung zu buchen.