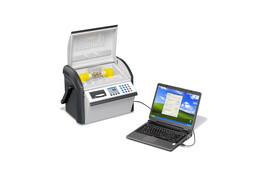
BAUR ITS Lite software
Measurement data management
for oil testers
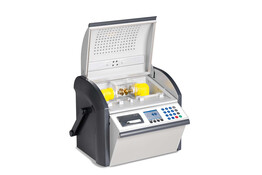
DPA 75 C
Oil breakdown voltage tester
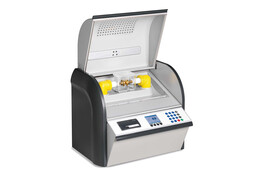
DTA 100 C
Oil breakdown voltage tester
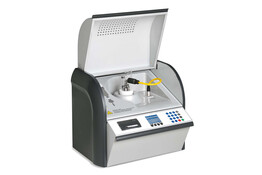
DTL C
Oil tan delta and resistivity tester
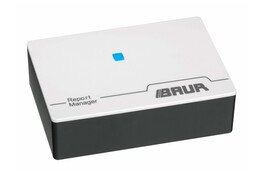
Report Manager
External USB interface
for BAUR oil testers